How does a vibrating road roller work?
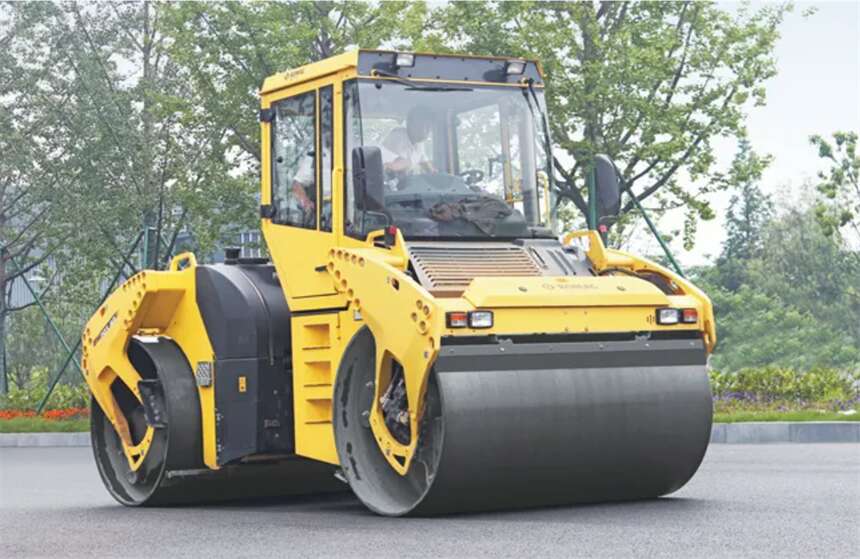
In the construction of highway engineering, the road roller is an indispensable construction machinery. Whether it is the compaction of the roadbed, the base layer or the surface layer, the road roller is inseparable. As one of the main compaction equipment in the current road construction, the vibratory road roller is generally It is divided into single-drum vibratory road rollers and double-drum vibratory road rollers. Single-drum vibratory road rollers are mainly suitable for the rolling of soil foundation, sand and gravel and base layers, while double-drum vibratory road rollers are mainly used for the rolling of asphalt layers. Vibration Road rollers are widely used in the construction of roads, municipalities, mines, dams and other industrial sites.
Compaction is the process of using external pressure to increase the compactness of the compacted material. Compaction in highway construction is to load the compacted material by external force, overcome the friction and adhesion in the material, remove the moisture and air, and reduce the particle void ratio. It is a way to increase the weight and density of the soil. Taking this measure can make the material particles form a dense whole, improve the stability and impermeability between the material and the base soil, and then meet the bearing capacity requirements of the road.
Vibratory rollers are commonly used equipment in road compaction. This type of equipment is generally equipped with amplitude devices and frequency modulation devices, which can achieve ideal compaction effects. Its working conditions can be adjusted according to compaction requirements. Compared with other types of road rollers, road rollers and light-duty road rollers have ideal economy and have been widely used in construction. The following is an analysis of the optimization of the working parameters of vibratory road rollers.
Analysis of working parameters of vibratory roller
When the vibratory roller is used in the construction process, its vibration will cause a reciprocating impact on the road surface. Under the influence of this impact factor, the static material will become a moving state, and the frictional resistance between the materials will also increase. The smaller the particles, the more closely connected the particles are, which can effectively improve the bearing capacity of the pavement. The degree of material compaction is closely related to two factors, the material properties and the technical parameters of the vibratory roller. In these two factors, the technical parameters of the vibratory roller include frequency, rolling speed, amplitude, static mass, vibrating wheel diameter, vibrating wheel width, vibration In addition to these factors, the number of wheels and static load, the number of rolling passes and rolling speed should also be considered.
Static mass and static load of vibratory roller
When carrying out the compaction work, the vibratory roller needs to apply its own static load and static mass factors. Under the working state, the vibration frequency will drive the particles to vibrate, so that the particles can be rearranged, and then the material density will be improved. Construction practice shows that the compaction energy of the vibratory roller is mainly determined by the vibrating wheel, and the weight of the vibrating wheel is proportional to the compaction depth of the roller.
Vibration frequency of vibratory roller
The vibration frequency is the number of rotations of the vibratory roller in one minute. The vibration frequency has an important influence on the compaction quality. In order to ensure the compaction energy, the frequency of the vibratory roller needs to be set to be consistent with the natural resonance frequency of the compacted material. If the frequency is too low, the It will cause the shock absorber block to resonate and damage the parts; if the vibration is too high, it will affect the reliability of the compaction result, and the ground will be over-rolled or severely impacted, resulting in uneven compaction.
Number of vibration wheels and driving form of vibratory roller
The working form of the vibratory roller is complex, and it is easy to cause the road surface to shift during the work process. The use of the driving wheel can effectively reduce the displacement of the road surface and improve the compaction flatness. Considering this factor, in order to ensure the compaction quality, it can be used Two-wheel drive road roller.
Rolling speed of vibratory roller
The rolling speed will affect the productivity of the road roller. In order to improve the productivity, scientific measures can be taken to increase the rolling speed of the road roller. When the speed is increased, it should also be controlled within a certain standard to prevent the impact of the compaction flatness.
Rolling times of vibratory rollers
At this time, rolling is closely related to the working parameters of the vibratory roller. At the same time, the state of the material will also affect the number of rolling. Therefore, it is necessary to scientifically control the number of rolling to ensure construction economy and material compactness.
Rolling material and rolling thickness of vibratory roller
Vibratory rollers have different requirements for the thickness of materials. Heavy-duty and medium-sized vibratory rollers are mainly used for compacting cohesive soils and clays with high plasticity. If the thickness of the rolling layer is too thick, the compaction degree will be affected to a certain extent. , the thickness of the lamination layer needs to match the function and quality of the roller.
Optimization method of working parameters of vibratory roller
Objective function of vibratory roller
When optimizing the working parameters of the vibratory roller, it is necessary to follow the principles of high efficiency and energy saving. On the premise of ensuring the compaction of the road surface, the number of compaction times should be reduced as much as possible. If the filler consumption is a fixed value, in order to reduce the number of compactions, the The working parameters need to be selected scientifically, so that the vibratory roller can play the most ideal compaction effect in the compaction process. The energy absorption of the exciting force can be calculated by the following formula:
Optimization of excitation frequency of vibratory roller
Different types of soil have different natural frequencies. According to the theory of resonance principle, when the excitation frequency is equal to or close to the natural frequency of the soil, a better vibration effect can be achieved. Relevant experiments show that in the specific application process, the excitation frequency of the vibratory roller needs to be set slightly higher than the soil frequency. It needs to be set between 25 and 30 Hz. When compacting the stable base of asphalt and mixture, the amplitude needs to be controlled at 0.4 to 0.8 mm, and the excitation frequency should be set at 33 to 50 Hz. Compaction experience has shown that excitation frequencies in this range can achieve good results. In the optimization of the excitation force amplitude, it should be noted that although increasing the amplitude can achieve a good vibration impact effect, if the amplitude is too large, it will easily lead to driver fatigue, damage to mechanical parts, and overvoltage. In reality, this also affects the compaction quality of the road surface. Therefore, the working parameters need to be set according to different types of rollers.
Optimization results of vibratory rollers
Under the compaction of the soil, its stiffness will become larger and larger, the damping will become smaller and smaller, and the optimal excitation frequency will also change to a certain extent. It can be in a critical state of vibration. After the soil becomes hard, the amplitude of the drum of the vibratory roller also begins to decrease. It can be seen that the tooling state of the vibratory roller belongs to high-amplitude work in the low-frequency state, and belongs to the high-frequency state. For low-amplitude work, under the influence of soil compaction change factors, the speed of the roller will remain between 2.5 and 4km/h, and the vibration pressure coefficient will also become smaller and gradually become stable.
Control of working parameters of vibratory rollers
In order to ensure the working quality of the vibratory roller, it is necessary to scientifically and reasonably control its working parameters. In the specific measurement and control system, the forms of sensors are various, and the commonly used are magnetoelectric speed sensors and moving magnetic speed sensors. The acceleration and displacement can be obtained only according to the differential and integral operations. The vibratory roller includes three pump systems. Among them, the driving pump is responsible for driving the walking motor, and the vibration pump is responsible for driving the vibration motor. As long as the opening of the vibration pump is changed, the rotation speed of the eccentric shaft and the excitation frequency can be changed, and can also be changed. The travel speed of the vibratory roller. In the amplitude modulation device, it is necessary to set the inner eccentric block and the outer eccentric inner sleeve, and change the axis of the inner eccentric block, so that the effect of adjusting the axis can be realized.
Conclusion
All in all, in the process of highway construction, it is necessary to select the relevant type of vibratory roller according to the actual situation of the construction enterprise and the requirements of highway construction. At the same time, the type of compaction object, material moisture content, material type, compaction thickness, construction On-site climatic environment, technical support conditions, maintainability, etc., take into account these factors to configure rolling equipment, strictly follow construction standards and specifications to carry out work, and improve the economy of construction.
Related Blogs |
Wow, this paragraph is fastidious, my sister is analyzing these things, thus I am going to tell her.
I am regular reader, how are you everybody? This paragraph
posted at this web page is actually fastidious.